Couple of things
Moray? is that correct. 2003'ish is that correct?
It is a transformer based psu rather than switched it is a 24 Volt 12 amp Lamda PSU I had spare. The blowing of the chips was when I was arcing up or, more when I can to the end of the cut I had an arc away from the cut edge and a dwell time to the plasma cutter was trying to arc into thin air and the HF would blow an axis. Put it this way I have spare units and chips now sat on my shelves just in case.
Robert, noted on the transformers if ever needed.
Not quite sure what you mean by how am I doing the THC, or perhaps I do I have not mentioned what I am using have I

I will copy what I have on another thread again in Mig welding
And as there some other like minded souls on here I thought I would share my thoughts so they can be picked over and comments raised.
When playing with my cut40, so I will assume very similar to cut50 etc. I found then when not cutting, i.e. the torch switch is off, the voltage at the terminals sits around -24 Volts ground to torch.
When cutting, the voltage can vary depending I guess on height, nozzle, speed etc on mine from around -85 Volts to -110 volts. The manual says it can go to 250 volts and I assume that is when it is trying to cut but the arc is broken and lastly on mine the manual says the rated voltage is 100 Volts.
So I read from that that I really want to keep the cutting voltage at 100 Volts, and that from what I have measured and assume, if I get less then 75 Volts I am probably driving the nozzle into the work piece and if the voltage was to go higher then say 125 volts I run the risk of breaking the arc.
I hope in my assumptions are OK so far ?
If I have read it correctly, THC controllers seem to provide 3 outputs: THC ON or ARC OK, move up, move down.
From my readings and figures above, I would say that if I can measure a voltage across the terminals of between 75 to 130 Volts, it must mean that the ARC is OK, in that it has an arc between torch and metal.
Then further to THC on, if the voltage goes above 101 Volts move the torch down and if the voltage goes above 99 Volts move the torch up. Guessing at a level of hysteresis here.
I would not like to be messing with anything that can reach over 100 Volts DC let alone the no load level of 250 Volts DC. So the output will get tapped with a resistive divider. To get me down to a respectable level I will probably consider a 10 to 1 divider, so 250 volts becomes 25 volts 110 to 10 etc.
Bring the voltage out of the plasma unit to a 4 way voltage comparator with relay outputs and set it up to provide THC on at a range of voltages between 7.5 Volts and 12.5 Volts.
Down at 10.1 Volts and up at 9.9 Volts.
I have a board from Ebay that looks like it may do the task
This is from the Ebay add.
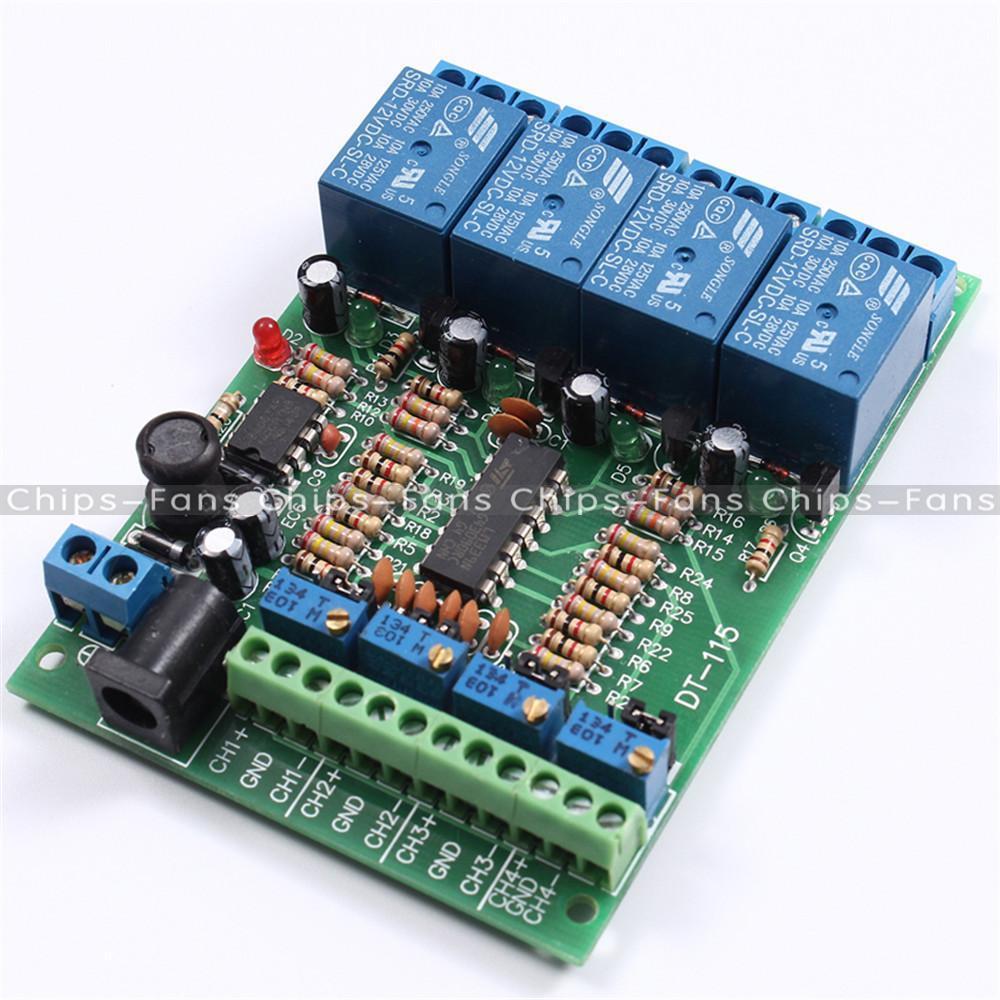
and cost less tan £10 delivered, has 4 inputs and drives relay outputs which means I should be able to keep things isolated.
It has a common ground between all inputs, has a 12 Volt input which provides an internal voltage of 31 Volts for the devices so can measure up to 30 volts.
Initial tests suggest it could work, but the idea is open to your thoughts.So that above is what I looked at doing and I am part way through. The psu for the comparator is a plugtop 12 volt unit that is fully isolated, from my junk box, the board was less than £10 and I have just bought a plastic box to fit it in so I do not short out on my welding bench, wires and most of the other parts I have.
If it does not work then less than £20 wasted, just time.
If it helps make the cut40 and CNC that little bit better because I have a bit more control and I am not dragging the tip all the time then that will be a reward.
Adrian